根據中國移動(dòng)機器人(AGV/AMR)產(chǎn)業(yè)聯(lián)盟數據,新戰略移動(dòng)機器人產(chǎn)業(yè)研究所統計,2021年工業(yè)移動(dòng)機器人主要市場(chǎng)占比中,汽車(chē)汽配行業(yè)占比為14.40%,仍然是移動(dòng)機器人移動(dòng)的主要市場(chǎng)。作為近幾年最受關(guān)注的移動(dòng)機器人細分品類(lèi)之一,無(wú)人叉車(chē)近年來(lái)在汽車(chē)汽配行業(yè)產(chǎn)線(xiàn)與倉儲的應用逐漸增多。以下盤(pán)點(diǎn)了未來(lái)機器人的6大經(jīng)典落地案例,看未來(lái)機器人如何突破場(chǎng)景難點(diǎn),充分運用無(wú)人叉車(chē)的技術(shù)優(yōu)勢賦能企業(yè)。
難點(diǎn)一: 密集型倉儲、突破舉升9.4米
為了提高存儲密度,有些倉庫采取密集存放的方案,這導致移動(dòng)機器人行駛路徑狹窄,同時(shí)還涉及到高位存儲。
未來(lái)機器人為華東某汽車(chē)零部件著(zhù)名生產(chǎn)廠(chǎng)商提供了智能化解決方案。
為提高車(chē)間運作效益,提高搬運效率降本增效,該企業(yè)聯(lián)手未來(lái)機器人,針對產(chǎn)線(xiàn)到產(chǎn)線(xiàn)和原料倉到產(chǎn)線(xiàn)的2個(gè)關(guān)鍵物流環(huán)節,部署了未來(lái)機器人前移式無(wú)人叉車(chē)和機器人管理系統。此項目的難點(diǎn)在于極限通道寬度內高達8.5米的5層貨架出入庫,該場(chǎng)景對于無(wú)人叉車(chē)的感知能力、精細控制和安全防護能力是較大的挑戰。
未來(lái)機器人采用前移式無(wú)人叉車(chē),最大舉升為9.4米,叉臂根部安裝了感知模塊,可以對橫梁狀況、庫位占用情況進(jìn)行安全檢測,為后續入庫作業(yè)提供信息輸入,克服高位庫視野盲區大的痛點(diǎn)難點(diǎn)。同時(shí),針對貨架老化變形、貨物存放位姿、貨物入叉位置等無(wú)人倉儲中影響安全作業(yè)的關(guān)鍵因素,未來(lái)機器人前移式無(wú)人叉車(chē)所具備了自適應模塊,可以很好地滿(mǎn)足多次重復精準叉取需求,克服了“貨物多SKU、中心不一”等困難,提高作業(yè)的安全系數。

難點(diǎn)二:全域智能管理、外設備自動(dòng)對接
全域智能管理與自動(dòng)對接外設備的難點(diǎn)主要在于,要求AGV本體企業(yè)的車(chē)體調度系統與中央控制系統有較高柔性,可以適配多種設備的不同軟件并進(jìn)行集成。
未來(lái)機器人已有相關(guān)全域智能規劃方案落地,系與華東某汽車(chē)零部件著(zhù)名生產(chǎn)廠(chǎng)商(與難點(diǎn)一同)聯(lián)手打造。
此次項目的場(chǎng)景中涵蓋多個(gè)自動(dòng)化設備,基地內車(chē)間之間有常閉的卷閘門(mén)作為間隔,每當貨物通過(guò)時(shí)都需要人工通知管理員開(kāi)門(mén),一旦人工響應不及時(shí),很容易因為人為原因造成貨物堵塞,嚴重時(shí)甚至影響生產(chǎn)效率。
未來(lái)機器人將機器人管理系統直接對接卷閘門(mén)控制系統,使得無(wú)人叉車(chē)行駛到卷閘門(mén)附近時(shí),系統提前發(fā)出指令到卷閘門(mén),避免了人工通知管理員開(kāi)門(mén)帶來(lái)的延遲和堵塞,進(jìn)一步提高生產(chǎn)效率。項目實(shí)施后,倉庫到車(chē)間、車(chē)間與車(chē)間之間的物流得到了無(wú)人化升級。由于無(wú)人叉車(chē)和智能管理系統的引入,實(shí)現了7*24小時(shí)不間斷物流作業(yè),大大的提升了供應鏈效率和靈活性。同時(shí),因為新技術(shù)的引用,出入庫準確率和作業(yè)安全性也得到了提高。

難點(diǎn)三:窄通道、0.1米轉彎半徑
很多工廠(chǎng)車(chē)間的現場(chǎng)通道空間非常有限,轉彎半徑過(guò)大會(huì )嚴重影響搬運的效率。讓平衡重無(wú)人叉車(chē)應用在窄通道場(chǎng)景中,行駛通道同時(shí)對行駛與轉彎半徑做出限制,將對車(chē)體的感知和定位精度和控制能力提出極高的要求。
未來(lái)機器人通過(guò)導入VNP15平衡重無(wú)人叉車(chē),為華北某汽配零件企業(yè)打造了平衡重叉車(chē)的窄通道場(chǎng)景應用案例。
項目實(shí)施難點(diǎn)在于客戶(hù)現場(chǎng)倉儲空間有限,項目現場(chǎng)貨架通道區域僅足夠一般的無(wú)人叉車(chē)運行,但通道寬度窄于平衡重無(wú)人叉車(chē)標準轉彎半徑。
未來(lái)機器人通過(guò)打磨產(chǎn)品高柔性核心能力,將轉彎半徑由原先的0.3m縮減到0.1m,同時(shí)提高無(wú)人叉車(chē)感知和定位精度和控制能力,成功實(shí)現0.1米轉彎內半徑,讓平衡重無(wú)人叉車(chē)也能完成窄通道內貨物存取。

難點(diǎn)四:載具種類(lèi)多樣標準載具和非標載具混場(chǎng)
汽車(chē)零部件種類(lèi)多達數千種,工藝生產(chǎn)流程繁雜,各個(gè)車(chē)間生產(chǎn)節奏不同,為汽車(chē)汽配行業(yè)實(shí)現柔性化的生產(chǎn)帶來(lái)更多挑戰。而汽配零部件種類(lèi)繁多、形態(tài)各異,專(zhuān)屬非標載具多,庫位管理混亂,不同載具的叉取方式與堆疊方式不盡相同,則要求無(wú)人叉車(chē)的叉取放置精度高,同時(shí)需要配備多傳感器。
未來(lái)機器人為某華南地區上市車(chē)企打造了多種載具混場(chǎng)的解決方案。
通過(guò)采用視覺(jué)+激光多種混合傳感器,未來(lái)機器人的無(wú)人叉車(chē)根據掃描提取的信息數據判斷相應的載具類(lèi)別,再通過(guò)自適應調整貨叉叉臂,提升末端操作精度與準確性,精準叉取載具。
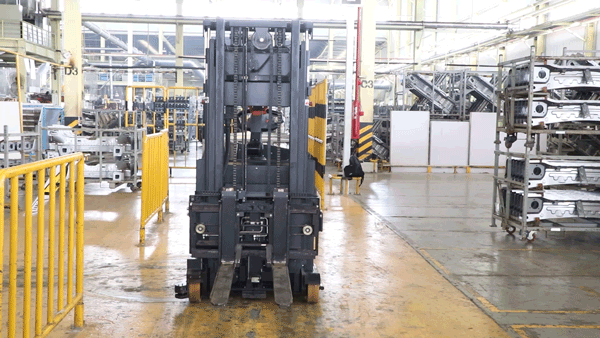
難點(diǎn)五:國內首例項目應用、六層以上料框精準堆疊
在倉儲籠六層堆疊中,要讓倉儲籠支架與下層精準對接,其叉取精度需要精確到毫米級。
未來(lái)機器人助力某國內車(chē)企制造基地打造智能物流模塊單元。
該企業(yè)制造基地占地面積約2000畝,車(chē)間生產(chǎn)根據業(yè)務(wù)波動(dòng)要求24小時(shí)作業(yè),工作時(shí)間長(cháng)、勞動(dòng)強度大,人員運維成本水漲船高,且為了提升倉儲效率,基地內采用倉儲籠多層堆疊方式,傳統模式中純人工搬運堆疊效率低,安全風(fēng)險大,倉儲籠四根支柱腳墩是人工插入支撐,存在支柱不穩定,高低不平整的現象,對無(wú)人叉車(chē)進(jìn)行堆疊作業(yè)時(shí)的末端感知控制精度要求極高;同時(shí),因零配件種類(lèi)繁多,車(chē)企貨物信息與物流信息在各個(gè)數據系統中難以及時(shí)同步,信息不對稱(chēng),貨物追溯難。
為有效解決客戶(hù)痛點(diǎn)難點(diǎn),未來(lái)機器人根據客戶(hù)需求實(shí)現生產(chǎn)車(chē)間物料自動(dòng)化搬運,在車(chē)間交接區、存儲區、待發(fā)區之間轉運,及完成2到6層物料堆垛。未來(lái)機器人通過(guò)配置2臺VNP15平衡重堆高式無(wú)人叉車(chē),實(shí)現24小時(shí)作業(yè)。
未來(lái)機器人VNP15平衡重無(wú)人叉車(chē)擁有高精度視覺(jué)伺服控制技術(shù),結合圖像識別計算,對倉儲籠支柱特征進(jìn)行信息提取、位姿計算,進(jìn)而精準叉取,降低人工堆垛帶來(lái)的安全風(fēng)險和貨損率;針對倉儲籠支柱高度不一的情形,無(wú)人叉車(chē)自動(dòng)開(kāi)啟高度自適應,通過(guò)一邊抬升貨叉一邊檢測插孔上方橫梁位置的方式,輸出檢測數據,從而對無(wú)人叉車(chē)的動(dòng)作進(jìn)行控制調整,完成六層精準堆疊。
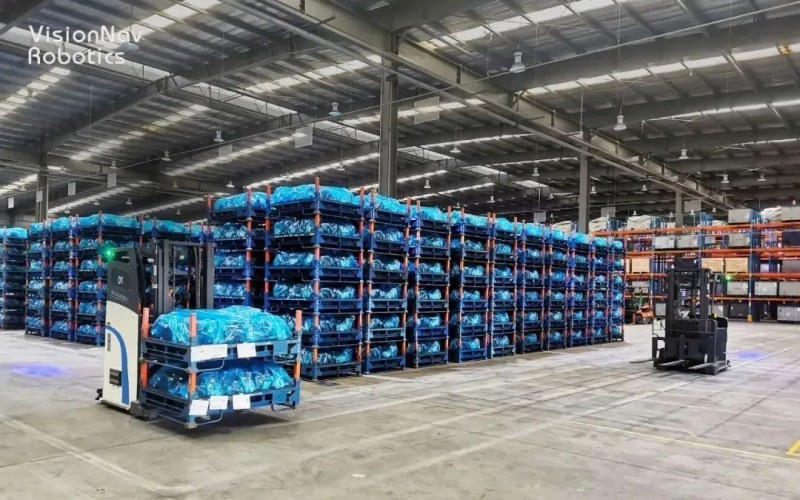
當有入庫需求時(shí),只需要給無(wú)人叉車(chē)下達作業(yè)指令,無(wú)人叉車(chē)收到指令后,將交接區兩托一疊的物料運至存儲區,堆疊至6托一疊,并同步更新 WMS庫位狀態(tài);出庫則是WMS下達出庫任務(wù),無(wú)人叉車(chē)通過(guò)中控調度系統接受任務(wù),將存儲區的6托一疊貨物,拆分成2托一疊,運送至待發(fā)區,并更新庫位空滿(mǎn)狀態(tài)。通過(guò)智能化物流模塊單元新升級,六層倉儲籠精準堆疊提升了3倍倉儲空間利用率,有效降低人工運維成本,解決了招工難題;中控調度系統與客戶(hù)項目系統的對接,貨物信息、庫位狀態(tài)、物流信息實(shí)時(shí)同步更新,讓貨物的入庫出庫更智能,管理更便捷,提升車(chē)間物流生產(chǎn)效率。
難點(diǎn)六:輪胎產(chǎn)線(xiàn)舊倉改造、跨樓層規劃
多層聯(lián)動(dòng)配合需要調度軟件的高度柔性,前期方案規劃工作量大,實(shí)施起來(lái)也具備一定難度。
2021年,未來(lái)機器人與世界前十、中國制造業(yè)500強的輪胎制造企業(yè)達成合作,為該企業(yè)某物流倉庫提供舊倉改造、自動(dòng)化升級的服務(wù),旨在全面提升倉庫的庫容和物流效率。
在此項目中,難點(diǎn)主要在:①跨樓層規劃。每層存儲區438*95m,面積較大,客戶(hù)庫容要求高,前期重新規劃庫位工作量大,且多層聯(lián)動(dòng)配合,要求自動(dòng)對接貨梯;②系統對接柔性高。對接既有WMS系統,承接大量SKU的入庫和出庫任務(wù),并對接產(chǎn)線(xiàn)機械臂和月臺裝車(chē)人工終端;③精度要求高。單料架貨物重量大(856kg),料架插孔開(kāi)口小、孔距不一,4個(gè)內扣型底座開(kāi)口小,要求自適應叉取并完成超過(guò)6層堆疊,作業(yè)精度要求高;效率要求高。出入庫節拍快,每天入庫11萬(wàn)個(gè)輪胎,出庫12~20萬(wàn)個(gè)輪胎。
客戶(hù)現場(chǎng)有兩個(gè)40000平米的存儲區,兩個(gè)存儲區均含多個(gè)樓層,客戶(hù)要求將入庫區的輪胎料架通過(guò)無(wú)人叉車(chē)自動(dòng)轉運至倉庫內部并進(jìn)行堆疊存儲,最高堆疊達6層;每個(gè)料架內僅存放同一SKU同一批次的輪胎。共計約1600種SKU,按照先進(jìn)先出的原則,根據訂單需求出庫至出庫區;以及空料架在庫內周轉搬運等流程。
綜合考量了項目規模與客戶(hù)預期,未來(lái)機器人為此次舊倉改造項目解決方案部署了多種類(lèi)型合計69輛無(wú)人叉車(chē)作為硬件支撐,同時(shí)配套了庫位管理系統、無(wú)人叉車(chē)中控系統等軟件集成,讓無(wú)人叉車(chē)具備自動(dòng)識別叉取位和自適應車(chē)身調整能力;采用任務(wù)串形式下發(fā)指令,實(shí)現了大庫位倉儲場(chǎng)景AGV無(wú)人叉車(chē)的多層聯(lián)動(dòng)配合,無(wú)人叉車(chē)中控系統的高計算力、多系統對接數以及兼容性讓AGV得以自動(dòng)對接貨梯、產(chǎn)線(xiàn)機械臂和月臺裝車(chē)人工終端,滿(mǎn)足了客戶(hù)生產(chǎn)節拍需求,革新了整個(gè)供應鏈管理流程,減輕了人工工作強度。
舊倉改造后,兩個(gè)存儲區合計存儲量將達到200萬(wàn)+個(gè)輪胎,增加了1.5倍庫容。7*24小時(shí)作業(yè),高強度作業(yè)環(huán)節實(shí)現“人工替代”,降低生產(chǎn)成本的同時(shí)提高了工作效率,完美承接了客戶(hù)需求的出入庫節拍,實(shí)現出入庫環(huán)節的全自動(dòng)、科學(xué)化管理。
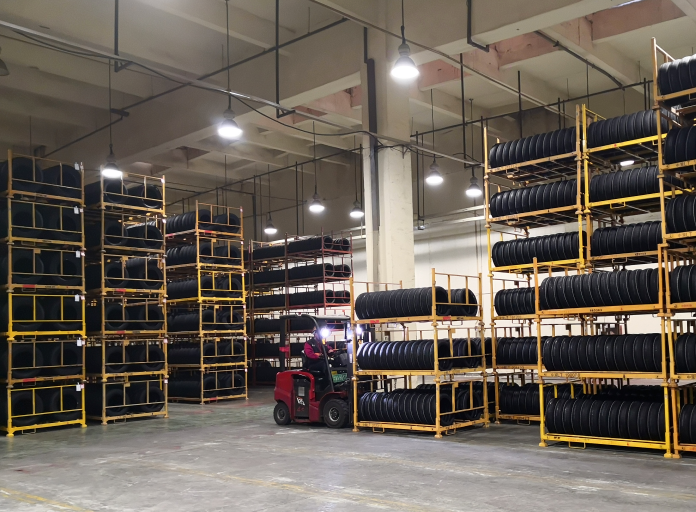
結語(yǔ):汽車(chē)制造廠(chǎng)的物流體系復雜,物流體量巨大,根據服務(wù)的目標不同,分為整車(chē)物流和零部件物流,其中零部件物流又可以細分為更多種類(lèi)領(lǐng)域。實(shí)現汽車(chē)制造工廠(chǎng)的智能化規劃需要從多方面逐步推進(jìn),不斷完善。未來(lái)機器人憑借著(zhù)獨特的技術(shù)路線(xiàn)和優(yōu)秀的物流無(wú)人化方案,在汽車(chē)汽配行業(yè)取得快速增長(cháng)。